Foundation Repair Bismarck ND is a crucial process that ensures stability and prevents damage to other areas of your home. It also protects and maintains your home’s value.
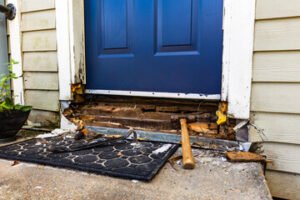
There is no clear line between what is deemed normal settlement and a need for foundation repair. It’s often a feeling.
During the process, homeowners can stay inside their homes. Here are some of the most common repair methods:
High-Density Polyurethane Foam is a modern, cost-effective solution for foundation repair that can be used for residential and commercial applications. It is injected into cracks or voids beneath sunken concrete, then expands and hardens to lift and stabilize the structure. This technique can be used to fix concrete sinking, basement floors, garage floors, sidewalks, driveways, and patios. The foam is made from a combination of petroleum-based polyol and diisocyanate, two chemical building blocks that form a durable, lightweight material. The foams are available in a variety of thicknesses, densities, and compression deflection values. They can also be modified with flame retardants to meet the requirements of specific applications.
Concrete lifting using polyurethane foam is faster and cheaper than traditional mudjacking methods. The injection process is 80% quicker, and the polyurethane material can be put back into service within minutes. This is because the injection holes required by urethane foam are only 3/8″ in diameter, which is significantly smaller than the injection holes required by other concrete raising methods.
Polyurethane foam is waterproof, which means that it will not be affected by the moisture content of the soil in which it is injected. This is important because excessive moisture can cause the concrete to crack and crumble, and it can also lead to deterioration of the reinforcing steel in the concrete. The fact that urethane foam is waterproof helps to protect the steel from corrosion and extend the life of the concrete.
In addition to its waterproof properties, urethane foam is also very strong and rigid. This makes it a good choice for structural support and a strong substitute for metal or wood. It is also much lighter than other concrete repair materials, which can reduce the overall load on a foundation and make it less likely to sink or crack over time.
If you’re facing issues with cracked, sunken or uneven concrete around your home, contact the team at Stabil Solutions today to find out more about how we can use polyurethane foam to raise and stabilize your concrete slab. Our innovative concrete repair services are faster, smarter, and more efficient than traditional mudjacking techniques, and we can help you achieve long-term stability and peace of mind for your home or business.
Mudjacking
Mudjacking is a concrete leveling and slab foundation repair technique that uses a mixture of water, sand and Portland cement to fill soil voids and lift sunken concrete. The slurry mixture is pumped under the concrete through holes that are drilled into the surface. The slurry expands to raise the concrete back into place, and the soil beneath is also filled so that future sinking is prevented. The process is quick and efficient, requiring no excavation or disruption of household living space.
Mudjacking can be used to repair a wide variety of concrete surfaces, including walkways, stoops and patios. It can also be used to lift garage floors, pool decks, driveways, slab homes and warehouse floors. It can be a more cost-effective solution than other methods of concrete foundation lifting, such as poly leveling or piles and piers. However, it is important to evaluate the extent of the problem and its cause before choosing this method of repair. If the underlying issue is not addressed, the concrete could sink again in the future.
Although mudjacking can be a good option for most concrete foundation problems, it is not recommended in situations with loose or unstable soils. It is also not appropriate for heavy structures like commercial buildings or houses. Furthermore, the slurry mixture can seep into porous or sandy soils and damage the structure underneath. It is important to hire a professional for a thorough inspection of the concrete and the soils in which it sits.
Another disadvantage of mudjacking is that it can leave behind unsightly holes in the concrete’s surface, and it requires drilling access holes that are bigger than those used for poly leveling. These larger holes can cause damage to the surrounding landscaping and may need patching after the repair. Additionally, sloping or uneven concrete creates tripping hazards and increases the likelihood of personal injury. Although mudjacking can raise concrete to eliminate these hazards, it cannot eliminate cracks or prevent them from recurring. If the sagging concrete is due to a weak or unstable soil, it is best to use a more permanent repair such as piers or pilings.
Concrete Piers
Concrete piers are a traditional repair method that offers stability and prevents future settlement. They’re also a good option for damp climates because they keep structures away from excessive water buildup, which could put pressure on the foundation and lead to further damage.
Concrete foundation piers are thick, heavy structural supports that can stabilize homes and other buildings even when the soil underneath is unstable. They are typically installed by excavating holes that are then filled with a mix of concrete and steel reinforcement. In some cases, a concrete post base is positioned in the center of the pier for added support and strength.
This repair technique is most commonly used for foundations that have settled or heaved, but it can also be used to lift structures like porches and sheds. Unlike other concrete repair methods, foundation piers are designed to stabilize and strengthen the entire structure, not just the affected area.
When selecting a professional for your foundation repairs, it’s important to choose a company with a solid reputation and experience. Check to see if they’re members of industry associations or have any certifications to demonstrate their commitment to excellence. You should also ask about their warranty period and aftercare services, as these can help protect your investment.
While a number of factors can affect which type of pier is best for your property, the length, weight, and location of your building are usually the biggest considerations. In general, concrete piers are better suited for lighter structures than steel ones. This includes sheds, shops, and small storage facilities. Steel piers are typically used to support larger structures, such as multi-story office buildings, skyscrapers, and data centers.
To install foundation piers, contractors use hydraulic jacks to drive the steel pipes into the ground until they reach the load-bearing strata beneath the structure. Once the piers are in place, they’re then used to lift the structure back to its original position. This process is repeated as needed to restore the foundation’s structural integrity and prevent further movement or damage. When properly inspected and maintained, piers can provide lasting stability and enhance the load-bearing capacity of your home or other construction.
Steel Piers
Steel piers are another cornerstone of modern foundation repair, providing stability to a building’s structure and re-elevating the concrete that has settled or sloped over time. The piers are made of high-strength steel and are designed for the specific soil conditions where they will be installed, meaning that you’ll get an expert solution that’s tailored to your unique situation.
Like concrete piers, the steel piers are driven into the ground beneath your home or commercial building’s foundation to transfer its weight from unstable surface soils to load-bearing soil or bedrock deep underground. As they are driven down into the earth, each pier interlocks with the next to create a strong, reinforced support column that is capable of bearing a significant amount of weight without shifting or settling.
Typically, the process starts with a site survey to locate where each pier will be installed and a complete excavation of each hole to allow for installation. Then, each pier is driven into the soil with a hydraulic jack and locked into place. Then, a hydraulic lift is used to raise or stabilize the foundation, depending on your specific needs.
The advantage of steel piers is that they are more durable and able to reach deeper into the ground than concrete piers, which means they have a greater load-bearing capacity and can resist environmental damage that affects other foundation materials. They are also a more cost-effective solution than other methods of repairing your foundation, and they have a low environmental impact.
Steel piers primarily fall into two categories: push steel piers and helical steel piers. The former uses steel pipes with plates attached to them, which are then hydraulically driven into the soil. The latter, on the other hand, consists of steel rods with metal plates attached to the end. They are screwed into the soil, similar to the way that helical anchors work.
Both types of piers offer superior strength and durability to ensure long-term stability for your foundation, making them the ideal choice for homeowners who need a permanent solution to their foundation problems. Contact us today to learn more about how steel piers can be used in your foundation repair and how they compare to other options.