Concrete polishing is a far more complex process than most people realize. It’s a technical job with multiple variables beyond the control of the contractor, which can significantly impact results.
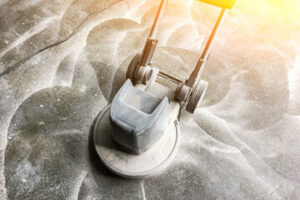
It’s important for a concrete polishing contractor to be honest with customers about timelines and expectations. Then they can help manage expectations and avoid miscommunication that can derail a project. Contact Concrete Polishing Contractor Waco TX for professional help.
When a contractor has extensive experience in concrete polishing, it shows that they’ve learned the ins and outs of the process. This knowledge is important because there are many variables that can affect the outcome of a project. Experienced contractors are more likely to understand these factors and be able to prevent them from occurring.
Whether you’re looking to make an impression on customers in a retail store, automotive dealership or hospital lobby, or improve worker morale in an industrial plant or warehouse, polished concrete is one of the most durable, cost-effective floor systems available. It also works well with a wide variety of colors and finishes to suit your space.
The basic polished concrete process involves a series of grinding steps to create a smooth, shiny surface. This is done with a machine that has diamond-segmented abrasives. During the grinding process, coarse abrasives are removed and replaced with finer grits until a high-gloss finish is achieved. It’s important that your contractor knows when to use each type of abrasive to get the best results.
If you’re building a facility with a large footprint, it’s essential that your concrete polishing contractor has experience working with other contractors to coordinate their schedules. This way, they can avoid overlapping and reduce the amount of time that your building is out of commission.
When you’re selecting a concrete polishing contractor, be sure to look at their past projects and read any online reviews they may have. This can help you gauge their level of expertise and determine if they’re the right fit for your needs.
In addition to having experience, you should ensure that the contractor has the proper equipment to perform the job. This includes grinders, vacuums, and dust control equipment. Additionally, they should be familiar with both wet and dry concrete polishing. This allows them to adjust the process as needed to achieve the desired result.
Lastly, they should be knowledgeable about the different types of sealers and staining options for polished concrete floors. For example, they should be able to advise you about anti-slip grit additives that can be added to the sealer to increase traction.
Certifications
Concrete polishing contractors specialize in upgrading worn down or new concrete floors to have a glossy sheen that looks like marble or granite. They can also apply a strong concrete sealer to the floor that will protect the polished surface and add durability. They can also add a variety of decorative finishes to the concrete such as staining, dying, or stenciling.
It’s important to choose a qualified concrete contractor that is certified by an established industry organization. For example, the American Concrete Institute and the American Society of Concrete Contractors provide standards for qualities such as concrete specular gloss/sheen8, distinction of image8, and aggregate exposure. By specifying a responsible concrete finishing contractor who follows these standards, specifiers ensure the results of the project will be consistent and accurate.
Qualified concrete polishing contractors are also able to identify and repair different types of concrete flaws. They can repair static cracks, or hairline fractures that only affect the surface of the concrete. They can also repair moving cracks or craze cracks by using a variety of cement-based patching compounds.
Concrete polishing is a science that requires experience and knowledge to achieve the desired results. The contractor must understand the sequence of grits that must be used to grind and refine the concrete to the level required by the design specification. The contractor must be able to choose the right amount of water to use during the grinding process for optimal results and to control silica dust exposure.
In addition to the scientific process of polishing, concrete polishing contractors must have the skills necessary to implement various surface treatments such as densifier products and sealers. The contractor must know how to assess the readiness of concrete for application based on its porosity and the concrete hardness, and understand how much product should be applied to the concrete to achieve maximum penetration and reaction.
The qualified contractor should be able to provide a comprehensive scope of work that clearly defines the job requirements and the schedule for completing the project. This document can help minimize misunderstandings throughout the project, especially when a change is requested by the client. This scope of work should also include clear instructions for preparing the concrete for the polishing process and for the curing period, as well as a hand off document that provides recommendations for maintenance of the floor once the job is completed.
Equipment
Concrete polishing is a complex and time-consuming process, and a professional contractor will use specialized equipment to ensure the results are of a high standard. This includes metal-bonded diamond abrasives that come in different grit levels to suit the surface type and degree of finish. For example, low grit pads are used for grinding and etching, while high-gloss polishing requires higher grit pads that produce finer and smoother particles.
A qualified contractor will also use a variety of other tools and products to enhance the beauty of polished concrete surfaces. This may include densifiers, which work by reacting chemically with the concrete to create a hard, dense, and durable substrate that resists water penetration, staining, and wear. They can be applied to new or existing floors, and they can help the polishing process go more smoothly as well.
Other important products a contractor will use include slurry vacuums and dust containment systems. Polishing can generate a lot of airborne dust that can be lethal if inhaled, so a contractor will need to have a way to keep the area clean and safe. Whether the polishing is done using the wet or dry method, a vacuum system will be necessary for containing the slurry and removing the abrasive dust particles from the surface as they are generated.
For decorative enhancements, a contractor can use dyes and stains to add color to concrete surfaces during the polishing process. They can even use stencils to create eye-catching patterns or unique colors and effects on the concrete floor. This can be an excellent way to make a warehouse or store look more inviting and appealing to customers.
A good quality polishing machine will feature a planetary drive and three or four smaller heads, known as satellite heads, that hold the diamond abrasives. These will rotate one way and the primary head will rotate the other, allowing a consistent and smooth rotation of the grinding pad to avoid leaving grind marks on the surface. A good polishing machine will also be able to operate on either the wet or dry method, and it should have a variable speed to allow the operator to match the grinding rate to the project specifications.
Safety
While it’s not necessarily glamorous work, a concrete polishing contractor must be prepared to face several safety hazards while performing their services. Grinding and polishing concrete requires the use of heavy equipment equipped with diamond-impregnated disks that grind down surfaces to a desired level of sheen and smoothness. This is not a DIY job and if you don’t know what you’re doing, you can easily cause damage to your concrete floors as well as yourself.
The first step in a successful concrete polishing project is clear communication with the customer. This involves a written scope of work that details what is expected to be completed. It should cover the entire process from start to finish, including what materials will be used and how long the project will take. The more detailed the scope of work, the less likely misunderstandings will arise during the course of the project.
A well-written scope of work will also outline the responsibilities of both parties. For example, who will move any structures that are going to be in the way of the concrete polishing process? What about dust mitigation and ventilation? This is an important document that should be reviewed and signed off on by everyone involved.
For facilities that rely on forklift and other industrial machinery, a polished concrete floor is an excellent option. The concrete is tough and durable, which reduces the risk of damage and improves the performance of industrial equipment. Additionally, it’s easy to clean and stain-resistant if the appropriate chemical treatments are applied.
Another benefit of concrete polishing is that it can be stained and dyed to add a customized look. This makes the flooring a more appealing choice to employees and customers. Dye can be added before or after the concrete is polished, but it’s important to test out a sample area beforehand so you can see how the color will look and if it will fade.
While polished concrete is a great option for many commercial and industrial uses, it’s not the best choice for every application. For example, food and beverage processing plants and pharmaceutical facilities have very specific needs that may be better served with specialized performance coatings. In these applications, chemical resistance is paramount and cannot be achieved with a traditional polishing process.